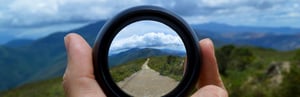
Apollo Optical Systems
Precision Polymer Optics From Concept to High-Volume Manufacturing.
World Leader In
Lens Design, Engineering, and Precision Polymer Optics
Apollo Optical Systems is one of the leading optics companies in Rochester, NY, delivering precision polymer optics for industries worldwide.
We specialize in injection molding of polymer optics in prototype to production volumes and single point diamond turning (SPDT). Our internal capabilities include optical/mechanical design and engineering, single point diamond turned optics, polymer injection molding, optical system assembly and extensive metrology and testing. Our team has vast experience in the lens design and manufacturing of diffractive and refractive optics.
More about Us
Our Core Markets
Apollo specializes in precision polymer optical components and subassemblies for the following core markets:
Automotive
Lightweight, impact-resistant polymer optics are advancing automotive technologies
Read More
Medical
High performance components for challenging optical requirements
Read More
Tactical
Flexible and lightweight polymer optics for precision tactical devices
Read More
Consumer
Custom optical components for AR/VR, cameras & more
Read More
Lighting
Versatile polymer optics for enhanced light control and efficiency
Read More Defense Durable optics for a wide range of defense systems & sensors Read More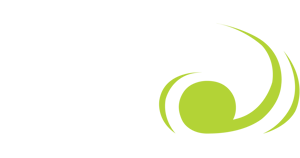
Need a Custom Optical
Component or Assembly?
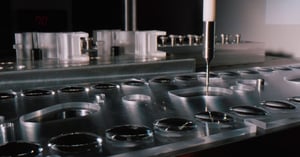