Plastic injection molding is the new industry standard for manufacturing plastic parts due to its quick turnaround, high-quality production, and cost-effectiveness. But even if this is the proper manufacturing process for your optical components, you still need to select the right plastic injection molder with optics experience to ensure a successful project.
Injection-molded parts have numerous benefits, but it’s a complex process. A lot can go wrong in conception, design, and production, so you must work with the ideal partner for your products, industry, and specifications. Here’s what you should look for:
Design Experience
Plastic injection molding is cost-effective, but only if approached with an eye for design. The design process is a critical stage in which you gain proof of concept and understand the strengths and limitations of your idea.
Choosing plastic injection molders with the right design team can ensure that your project has the suitable materials and approach to meet your specifications, performance expectations, and budget. If there are issues at this stage, a design team with experience can strike the perfect balance between different aspects of the project.
Volume Specialization and Capacity
There are thousands of injection molders in the US, so it can seem overwhelming to determine who’s the best choice for you. One of the crucial considerations is the company’s volume specialization and capacity.
If you’re creating a system or component for mass production, you will need a molder who can handle that capacity without sacrificing timeline or quality. Low- to moderate-volume molders often have a limit of 10,000 units or fewer. In addition, they may not have the proper equipment to handle the production numbers, leading to a higher project cost for you.
If your project needs hundreds of thousands of parts, such as aerospace, agriculture, or medical device optics, you will need a high-volume molder equipped to tackle mass production. These molders can often work with projects that require 750,000 parts or greater.
Material Familiarity
Whether working with only FDA-approved plastics or a different polymer for its specific capabilities, you want to work with a plastic injection molding partner who understands each polymer’s strengths, weaknesses, and applications.
Different plastic resins have other properties in moldability, flexibility, strength, durability, heat resistance, and more. An experienced injection molder should be able to guide you in choosing suitable plastic resins for your application and discuss how the material will impact your optical surfaces.
Specification Requirements
You’re fortunate if you can design your project and manufacture it according to the initial specifications. Often, product manufacturers have to compromise on the specifications required to meet the performance needs, budget, or materials.
When you work with an expert plastic injection molding company, you benefit from years of experience bringing concepts to life. They can prioritize your project demands and recommend the best alterations or materials to get it as close to your original vision as possible.
Tooling Requirements
Optical plastic injection molding requires mold tools that are orders of magnitude more precise than standard injection mold tooling. Single-point Diamond Turning machines provide the necessary precision for the optical surfaces. In addition, specialized metrology is also needed to ensure the accuracy of your optical surfaces. Discuss your optical requirements with your molder to make sure they have the capabilities required.
Quality Assurance
One of the enormous benefits of plastic injection molders is that they can cost-effectively create high volumes of identical parts. Though the process ensures that your components will all look, behave, and perform the same, quality assurance is vital for monitoring the process and reducing the risk of issues.
Quality assurance comes down to many factors, including the quality of the machinery, the project management and software, the materials, the mold maintenance, and the inspection process. A plastic molding company that takes quality assurance seriously will have an ISO certification and quality assurance systems to produce high-quality parts.
Timeline
Time is an important consideration when you’re manufacturing plastic molded parts. The design process can take a lot of time to adjust the components to your specifications. Then once the molding begins, it can take weeks or months to complete.
Mold designers must consider the timelines for design, design revisions, prototyping, and more. Delays or obstacles should be factored into this timeline, including issues like shipping delays, shortages of the necessary polymers, equipment repairs, etc. If you have time constraints for your project, discussing that upfront is essential to understand production capacity and get a realistic timeline estimate.
Strategic Fit
Whether you’re looking for a long-term molding partner or working on a one-off project or component, knowing that you’re working with a manufacturer who’s a strategic fit for your company is essential.
Look for companies with a positive reputation in the industry, exceptional customer service, and shared organizational value. You should also pay attention to companies with a long-standing reputation for industry excellence.
Choose Apollo Optical Systems for Your Optical Components
Apollo Optical Systems is an industry leader in designing and manufacturing custom optical components. Our polymer injection molding technology is fine-tuned to create consistent, high-quality parts that meet or exceed industry standards. Contact us today to discuss your custom optics project!

About Dale Buralli
Dr. Dale Buralli has served as the Chief Scientist for Apollo Optical Systems since 2003. In this role, Dr. Buralli is responsible for the design and optical modeling of various optical systems. These systems include virtual or augmented reality, ophthalmic and other imaging or illumination systems. Additionally, he provides support for optical tooling of lens molds and prototypes, including the development of custom software for both production and metrology. Dr. Buralli got his Ph.D. in optics from the University of Rochester in 1991. Now he is an Adjunct Professor of Optics at the University of Rochester’s Institute of Optics.
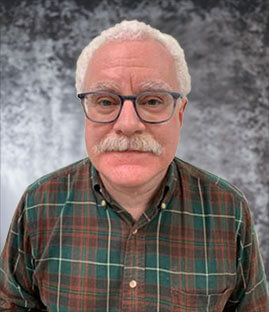