Precision molded components are made by molding either silicone or plastic in a particular way to produce a part with a high degree of accuracy and tight tolerances. The molding process is made to be repeatable in long machine runs.
The precision molding process isn’t used for the entire production process. Instead, it is only necessary on occasion for the manufacturing process for products that include highly precise forms of plastic injection molding.
About Precision Molds
Precision injection molding is a highly technical process that requires specialty precision molds and precision molding machines.[1] It differs from conventional injection molding and is typically used only for precise plastic parts with complicated geometry.
The precision mold dictates how precise the finished product turns out. The following factors influence how precise a finished product is:
- The precision of the mold cavity size
- The precision of the parting surface
- The accuracy of the cavity position
- The dimensional tolerance of general precision molds
- The choice of materials
- The number of cavities in the mold
- The runner size
- The material of the precision mold
- The thickness of the plates and cavity wall
- The expertise of the design engineering
Precision Molding Process
Precision molding is the process of molding plastic into calculated shapes using CNC machining. As technology advances and becomes more sophisticated, the industry needs more sophisticated molding processes to create precision parts for medical devices, IT, automotive applications, and pharmaceuticals.
Here are some benefits of precision molding:
- The process offers enhanced solutions to issues that often occur in the manufacturing of technical products
- The process can be less expensive than other processes
- The research and development into precision molding allows the development of precision components with high quality and precision at lower costs.
- Precision molding is ideal for mass production and is available at lower costs than manual molding.
- The polymer optic in precision molding is necessary to develop high precision components with unique edges.
- Precision molds allow for integrated optical and mechanical functionality
- The cycle time is lower than other molding processes
- The process allows for production in many shapes or designs without added costs
Automating the Precision Molding Process
One of the most significant benefits of precision molding is its potential for automation. The whole process can be automated and customized through software programs for efficient manufacturing.
The precision molding and design engineering process is conducted through cells that can also handle injection molding, coating, testing, and more, all using computer programs.
With automation, precision molds can be fitted with mechanical mounts, such as snappers or lens mounts. These components can be installed or removed as needed.
Things to Consider with Precision Molds
Tolerances
Precision molding is not used on the entire structure of a product, but only on the parts that require high precision. This applies to components that have tight tolerances, which means the manufacturer needs to follow the requirements precisely to ensure the component doesn’t damage the injection molding equipment.
The development of the entire product using precision molding is costly and could be a waste of money. It’s reserved for only the necessary parts that require high precision. It’s vital that the designer understands the precision requirements to ensure cost-effectiveness.
Materials
The molding materials for precision molding are different from other molding types due to unique factors. Precision molding can cause shrinkage in plastic and requires molding materials with high tolerance.[2]
Precision molding may require a shrinkage of +/-0.002, so ABS plastic and polyethylene (two materials often used for molding) are not suitable.
In many cases, manufacturers add glass or resins to the plastic to keep the plastic in place and absorb heat, reducing shrinkage. There’s no guarantee that the material will not still shrink, however.
Technique
Precision molding requires all product components to be produced identically and fitted together identically. If a product is not identical in the mold design, the corresponding precision product will not be accurate.
This is also a slow and patient process that requires time and focus. It’s important to choose a company with extensive knowledge and experience in precision molds – not just any optics manufacturer will do.
Precision Molding Equipment
Precision molding machines are a vital part of the precision molding process. These machines should be highly pressurized to improve the precision and quality of the finished product. With the right machine, the mechanical strength of the part increases while reducing the shrinkage factor.
These machines should also be able to manage the repeatability and accuracy of the product to produce identical components.
Choosing a Manufacturer
Precision molding is more expensive and sophisticated than other types of molding. But it’s necessary for specific optical components. Therefore, it’s vital to choose the right manufacturer for precision molding to ensure you get the performance and specifications you want.
Here are some things to consider:
- Choose the right designer: Precision molding requires a thorough understanding of the custom optics components and which parts require high tolerance. An experienced designer can help you determine which tolerances conventional injection molding can manage and which should use precision molding to keep the project cost-effective.
- Choose the suitable material: The right resins are fundamental to the success of your precision molded parts and determine the success of the finished product. This ultimately comes down to shrinkage and the addition of fillers to combat this. An experienced manufacturer will have a deep understanding of choosing the right materials and filler materials to lower the shrinkage range and create a component with the ideal structure.
Choosing a precision molding manufacturer plays a significant role in your molded components. Select a manufacturer specializing in high precision molding and tooling to produce high-quality, identical parts.
Precision Molds from Apollo Optical Systems
If you need consistent, high-quality parts and components that meet or exceed industry standards, choose Apollo Optical Systems. We work with our clients through the entire process to ensure they can create polymer-based optical products to their exact specifications. Contact us today to discuss your custom optics design!
Sources:
[1] https://www.sciencedirect.com/science/article/abs/pii/S0141635922000319 [2] https://www.ncbi.nlm.nih.gov/pmc/articles/PMC7603191/

About Dale Buralli
Dr. Dale Buralli has served as the Chief Scientist for Apollo Optical Systems since 2003. In this role, Dr. Buralli is responsible for the design and optical modeling of various optical systems. These systems include virtual or augmented reality, ophthalmic and other imaging or illumination systems. Additionally, he provides support for optical tooling of lens molds and prototypes, including the development of custom software for both production and metrology. Dr. Buralli got his Ph.D. in optics from the University of Rochester in 1991. Now he is an Adjunct Professor of Optics at the University of Rochester’s Institute of Optics.
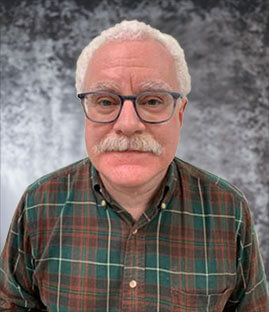