Custom optical and mechanical design is a sub-discipline of optical engineering that uses optics, such as lenses and prisms, to form an optical instrument within mechanical structures. Correct and stable positioning of the optical elements is required to ensure the optical system performs as intended.
Generally, the design process begins with recognizing a need for a device and moves through the concept and prototyping to final production and assembly phases.
During this process, optics are tested to ensure the design is operational and without flaws that may inhibit performance under certain conditions, such as extreme temperatures, vibration, or shock. This helps designers determine the best materials and design features.
Making the right choices in the design phase involves interdisciplinary teams and their areas of expertise. These may include structural design, mounting, lens-to-mount surfaces, materials, and assembly.
Considerations in Custom Optical and Mechanical Design
Choosing Materials
The materials used for an optical design are crucial to the performance and budget. With the wrong materials, a system won’t meet the desired specifications or may be cost-prohibitive.
Another consideration is weight. If material properties and costs are agreeable, the choice between them may depend on the density due to its impact on the total weight of the final product. Ultimately, the weight of the optical component may affect the mechanical mounting.
Developing Structural Design
An optical system is complex and relies on every component resting in its intended place and orientation. Gravity, temperature changes, and other external forces can distort the surface and affect the system’s function.
Structural designs must be stable enough to weather these effects throughout the operating cycle. The optics must have enough stability to stay in their place in extreme environmental conditions like shock, vibration, or extreme temperature fluctuations. In many cases, small deflections are acceptable through the full operating range, as long as the components remain intact and return to their optimal position.
The structure should be designed for maximum stability and stiffness to reduce deflection from external forces but not so constrained that the optical component becomes damaged or irreversibly displaced from slight fluctuations.
Choosing Lens-to-Mount Surfaces
The lens mount and positioning are vital to the performance of many optical systems. While metal surfaces are ideal for mounting the polished surfaces of lenses, glass-to-glass mounting is not the best choice.
Lenses should be preloaded axially to withstand maximum acceleration loads in extreme temperatures.1 Fluctuation in temperature can impact preloads. If needed, ring-flange axial constraints can provide tighter control of axial force.
All lens-to-mount surfaces should be designed for low axial contact stress. This means that:
- Conical metal surfaces can touch convex lens surfaces tangentially
- Convex toroidal surfaces can touch concave lens surfaces
- Flat metal surfaces can touch flat bevels on lenses
For systems with severe radial accelerations, the lens rim should be constrained within the mount. Spacers can help to fill gaps.
Managing Stray Light
Stray light is any light that is not accounted for or intended in an optical system.2 Even small amounts of stray light can cause undesirable effects like multiple images, reduced contrast, or, in the case of high-powered lasers, glass failure.
Because of this, stray light analysis is vital to testing an optical system. If stray light is a problem, several interventions can eliminate the light or mitigate its effects. Using apertures will block stray rays, as will anodizing mounting components or coating them in black oxide, depending on the material. Blackening lens edges can also mitigate stray light.
Most stray light issues are identifiable in the design phase, but these interventions can mitigate or eliminate stray light that remains in the production process.
Determining Assembly and Alignment
Accurate assembly and alignment are critical to system performance. Each previous step of the process is working toward success in this step.
Before assembly, the design team must clean and dry all components. From that point, they will need to use only specific lubricants that have met quality approval. The team must align optics first, after which they can lock adjustments into place with clamps, epoxy, welding, or soldering.
After completing assembly and alignment, the team may seal optical instruments to protect the optical components from moisture and debris. During future maintenance, they will need to clean components with dry nitrogen or helium.
Custom Optical and Mechanical Design
Each step of the optical and mechanical design process is key to optimal system performance. At Apollo Optical Systems, we understand optical and mechanical design fundamentals and how it impacts the final product’s performance. If you have a custom optical design in mind, we’re here to help with all phases of the development cycle. Contact us today to discuss your idea!
Sources:
[1] https://wp.optics.arizona.edu/optomech/wp-content/uploads/sites/53/2016/08/26-Mounting-of-lenses-1.pdf [2] https://www.spiedigitallibrary.org/conference-proceedings-of-spie/10569/105691A/Fast-and-accurate-modeling-of-stray-light-in-optical-systems/10.1117/12.2307936.full?SSO=1
About Dale Buralli
Dr. Dale Buralli has served as the Chief Scientist for Apollo Optical Systems since 2003. In this role, Dr. Buralli is responsible for the design and optical modeling of various optical systems. These systems include virtual or augmented reality, ophthalmic and other imaging or illumination systems. Additionally, he provides support for optical tooling of lens molds and prototypes, including the development of custom software for both production and metrology. Dr. Buralli got his Ph.D. in optics from the University of Rochester in 1991. Now he is an Adjunct Professor of Optics at the University of Rochester’s Institute of Optics.
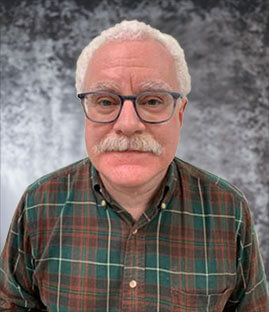